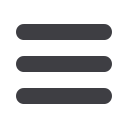
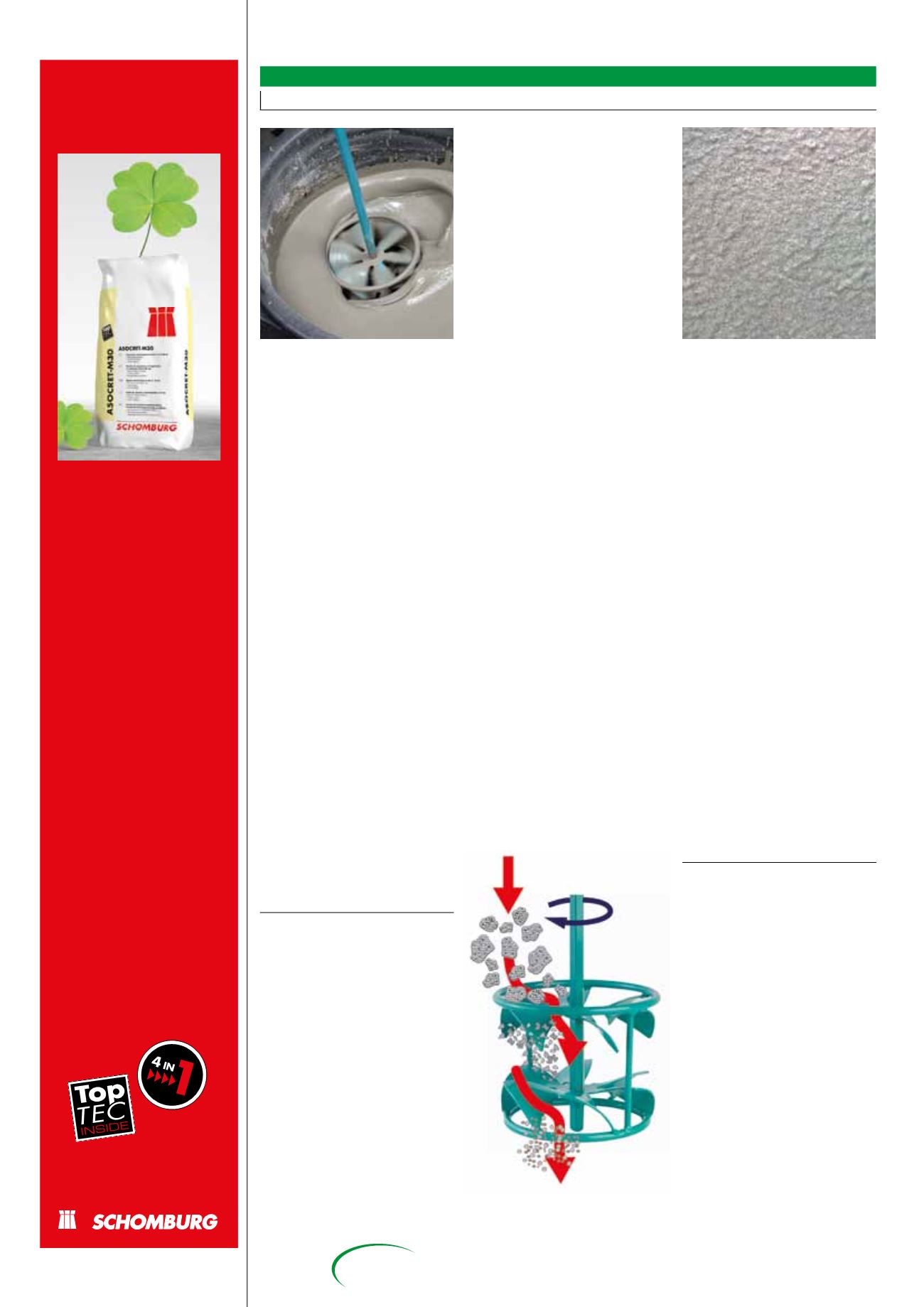
Schützen & Erhalten · Juni 2016 · Seite 12
Fachbereiche
Bautenschutz
Bild 2: Mischwirkung DLX.
Drehzahl und Kraft besitzen. Erfah-
rungsgemäß sind 600–800 U/min
erforderlich. Vielfach werden dop-
pelläufige Wendelrührer (handge-
führte Zwangsmischer) zur Aufbe-
reitung der Komponenten genutzt.
Die vorgegebenen Mischzeiten der
Hersteller sind unbedingt einzuhal-
ten und dürfen nicht unterschritten
werden. Ebenso ist die Wasserzuga-
be in vorgegebener Menge in Liter
angabe genau einzuhalten. Hierfür
sind auf der Baustelle Messbecher
bzw. Messeimer vorzuhalten.
Die genaue Wassermenge und
die Aufbereitung hat entscheidende
Auswirkung auf die zu erwartende
Dichtheit der MDS. Bei Nichtein-
haltung der Wasserangaben und der
produktspezifischen Mischempfeh-
lung kann MDS nicht optimal auf-
bereitet werden. Die Folge ist, dass
die Dichtheit nach dem Erhärten und
damit die zugesicherten Eigenschaf-
ten nicht erreicht werden können.
Durch Überwässerung − einen zu
hohen Wasserzementwert − wird das
Schwindverhalten von ≤2,5mm/m
negativ beeinflusst und die MDS ist
rissgefährdet.
Mischfehler
Des Weiteren kann es bei der
Aufbereitung, dem Mischen der
Komponenten, zu folgenden Fehl-
stellungen kommen:
–
–
Rührbehälter zu klein
. Der
Mischeimer sollte so gewählt
werden, dass der Rührer im-
mer vollständig vom Mischma-
terial bedeckt ist. Ragt dieser
aus dem Material heraus, so
wird dieses hochgeschleudert
und verschmutzt den Misch-
platz.
–
–
Reihenfolge der Material-
zugabe nicht beachtet
. Erst
die Flüssigkomponente in das
Mischgefäß vorlegen, anson-
sten kann es zur Nichtbenet-
zung kommen und es bilden
sich Klumpen oder Anhaf-
tungen, die sich nicht mehr
auflösen.
–
–
Falsches Rührwerkzeug.
Das
Zementpulver lässt sich nicht
untermengen, bildet bei Kon-
takt mit Wasser schnell Klum-
pen, die nicht mehr aufberei-
tet werden können.
–
–
„Nach oben statt nach un-
ten gemischt.“
Der einge-
setzte Rührer hat eine falsche
Mischwirkung. Das Fördern
des schweren Materials wäh-
rend des Mischens ist sehr
mühsam. Das Rührwerk drückt
sich aus dem Material,am Ei-
merboden befinden sich tro-
ckene, nicht vermischte Mate-
rialrückstände.
–
–
Mischzeit
. Die Produkteigen-
schaften des Materials kom-
men nicht zur Entfaltung. Pro-
duktqualitäten können nicht
erreicht werden. Mit zu ge-
ringer Mischzeit kommt es
zu mangelnder Haftfähigkeit
der MDS auf dem Untergrund,
Hohlstellen oder Abplat-
zungen sind oft auf unzurei-
chende Durchmischung zu-
rückzuführen. Des Weiteren ist
auf eine Hersteller abhängige
Einhaltung einer Reifezeit
nach dem Mischen und er-
neutes Aufschlagen produkt
abhängig zu achten.
–
–
Mischen mit zu geringer Ge-
schwindigkeit.
Der Kraftein-
trag in die MDS reicht nicht
aus, um die Flüssigkeitsbe-
standteile mit den Feststoff-
komponenten zu verbinden.
Dieses führt zu einem höheren
manuellen Verarbeitungsauf-
wand. Zu sehr spritzende MDS
können zu Stopfern im Spritz-
aggregat führen.
–
–
Reinigung wird vernachläs-
sigt
. Ablagerungen wie an-
getrocknete Rückstände am
Rühreinsatz lösen sich beim
nächsten Mischvorgang ab.
Sie lösen sich nicht auf und
bilden in der Mischung uner-
wünschte Fremdkörper, die zu
Fehlstellen und Durchfeuch-
tungsschäden führen können.
Erfahrungsgemäß haben sich zum
Mischen Mineralischer Dichtungs-
schlämme sowie verlaufsfreund-
licher Materialien wie Verguss-,
Nivellier- und Spachtelmassen Rüh-
rer mit übereinander gelagerten
Turbinenschaufeln in der Fachwelt
bei einwandfreier Durchmischung
von Flüssig- und Pulverkomponen-
ten etabliert. Die Aufbereitung er-
folgt von oben nach unten.
Verarbeitung
Mineralische Dichtungsschläm-
men können gestrichen, gespachtelt
oder mit geeigneten Spritzgeräten
gespritzt werden. Mauerquaste,
Deckenbürsten eignen sich zum
Streichen. Glättkellen oder Schicht-
dicken- und Zahnkellen werden
zum Erreichen der entsprechenden
Frischschichtdicken genutzt. Hierbei
wird der MDS-Auftrag unmittelbar
nach dem Auftrag verschlichtet/ge-
glättet. Zum Spritzen werden Schne-
ckenpumpen oder Peristaltikpumpen
eingesetzt. Die Pumpe fördert das
Material, im dichten Strom und im
Spitzrohr wird Druckluft in das Ma-
terial eingeleitet und die MDS wird
an die Bauteiloberfläche appliziert.
Bei Arbeitsunterbrechungen
muss die MDS auf 0 ausgezogen
werden, um bei Wiederaufnahme
www.schomburg.de SPART ZEIT & GELD! ASOCRET-M30 Der universelle Sanierungsmörtel Spachtelmasse, Reparatur- mörtel, Sperrputz oder Hohl- kehlenmörtel - ASOCRET-M30 ist der EINZIGE Sanierungsmörtel, der ALLE VIER PRODUKTE IN EINEM VEREINT GLÜCK GEHABT: 4 PRODUKTE IN EINEM!Bild 4: MDS Oberfläche, gespritzt.
Bild 3: Mischprinzip von oben nach
unten.